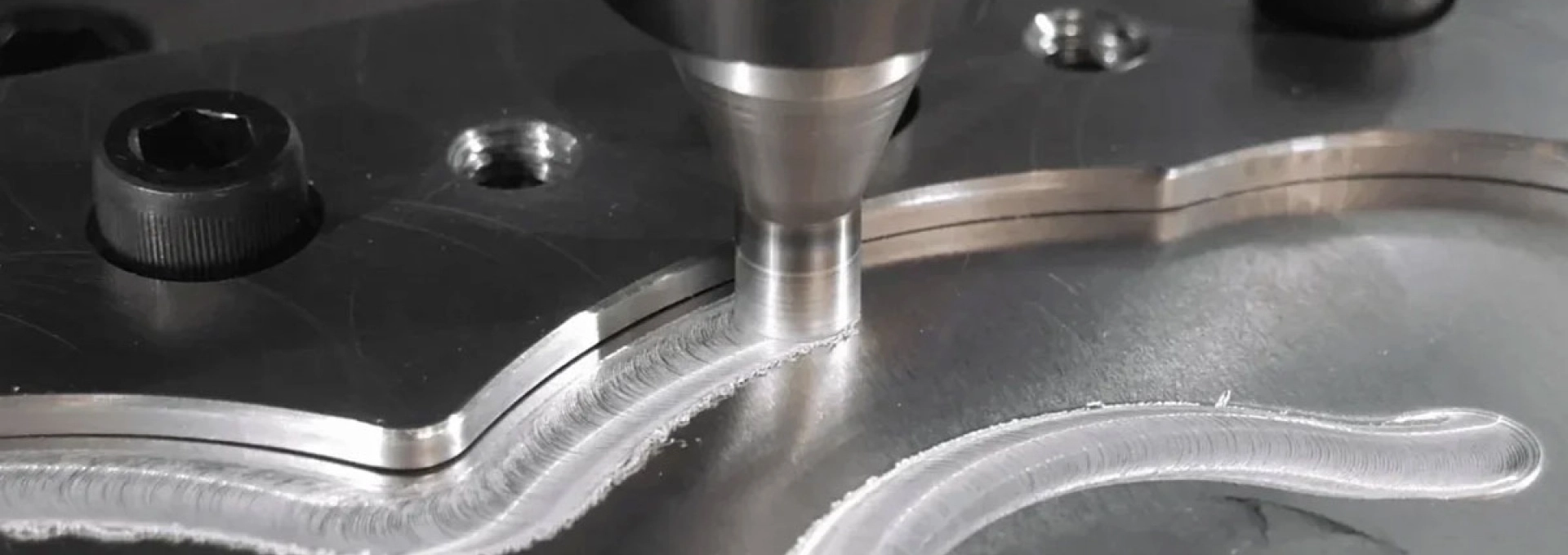
Friction stir welding (FSW) has revolutionized the joining of materials, particularly in industries where high-strength, lightweight connections are crucial. This innovative solid-state welding process, developed in the early 1990s, offers significant advantages over traditional fusion welding techniques. By leveraging the heat generated from friction and mechanical stirring, FSW creates high-quality joints without melting the base materials. Its ability to join dissimilar metals and alloys, coupled with reduced distortion and improved mechanical properties, has made it a go-to method in aerospace, automotive, and marine applications.
Fundamentals of friction stir welding (FSW) process
The friction stir welding process relies on a non-consumable rotating tool that generates frictional heat and induces plastic deformation in the workpiece materials. This tool, consisting of a shoulder and a pin, plunges into the joint line of the materials to be welded. As it rotates and traverses along the joint, it creates a plasticized region of material that is mechanically mixed and forged together, forming a solid-state bond.
One of the key advantages of FSW is its ability to join materials that are challenging to weld using conventional fusion techniques. This includes high-strength aluminum alloys, magnesium alloys, and even dissimilar metal combinations. The process occurs below the melting point of the materials, which eliminates many of the defects associated with fusion welding, such as porosity and hot cracking.
The FSW process can be broken down into four main stages:
- Plunge stage: The rotating tool is pressed into the workpiece until the shoulder makes contact with the surface.
- Dwell stage: The tool remains stationary for a short period to generate sufficient heat through friction.
- Welding stage: The tool traverses along the joint line, mixing and forging the plasticized material.
- Tool withdrawal: The tool is retracted from the workpiece, leaving behind a solid-state weld.
Understanding these stages is crucial for optimizing the FSW process and achieving high-quality welds consistently. The interplay between tool design, process parameters, and material properties determines the final weld quality and performance.
FSW tool design and material selection
The design and material selection of the FSW tool are critical factors in the success of the welding process. The tool must withstand high temperatures and forces while effectively generating heat and facilitating material flow. Tool geometry significantly influences weld quality, process efficiency, and tool life.
Shoulder geometries: concave, convex, and scrolled
The shoulder of the FSW tool plays a vital role in heat generation and material containment. Three primary shoulder geometries are commonly used:
- Concave shoulders: These provide good material containment and are widely used for flat plate welding.
- Convex shoulders: Offer improved heat generation and are suitable for welding materials with different thicknesses.
- Scrolled shoulders: Feature spiral grooves that enhance material flow and can reduce surface defects.
Each shoulder design has its advantages and is chosen based on the specific welding application and material properties. For instance, scrolled shoulders are particularly effective in reducing flash formation and improving surface finish in aluminum alloy welding.
Pin profiles: cylindrical, tapered, and threaded
The pin, or probe, is responsible for material stirring and plays a crucial role in weld formation. Common pin profiles include:
- Cylindrical pins: Simple and effective for many applications, particularly in thinner materials.
- Tapered pins: Provide improved material flow and are suitable for thicker plates.
- Threaded pins: Enhance vertical material movement, resulting in better mixing and weld quality.
Advanced pin designs may incorporate features such as flats, flutes, or stepped geometries to optimize material flow and reduce welding forces. The choice of pin profile depends on factors like material thickness, alloy type, and desired weld properties.
Tool materials: PCBN, tungsten carbide, and tool steel
The selection of tool material is critical for ensuring tool durability and maintaining weld quality. Common tool materials include:
- Polycrystalline Cubic Boron Nitride (PCBN): Offers excellent wear resistance and thermal stability, ideal for high-temperature applications.
- Tungsten Carbide: Provides good wear resistance and is suitable for welding aluminum alloys and other softer materials.
- Tool Steel: Cost-effective and widely used for welding aluminum alloys, but may have limitations in high-temperature applications.
The choice of tool material depends on the workpiece material, welding parameters, and production requirements. For instance, PCBN tools are often preferred for welding high-strength steels due to their superior wear resistance at elevated temperatures.
Wear-resistant coatings for FSW tools
To enhance tool life and performance, wear-resistant coatings are often applied to FSW tools. These coatings can significantly improve tool durability, reduce wear, and maintain consistent weld quality over extended production runs. Common coating materials include:
- Titanium Nitride (TiN): Offers good wear resistance and reduces friction.
- Titanium Aluminum Nitride (TiAlN): Provides excellent high-temperature stability and oxidation resistance.
- Diamond-Like Carbon (DLC): Offers low friction and high hardness, suitable for welding abrasive materials.
The selection of an appropriate coating depends on the specific welding application, workpiece material, and operating conditions. Proper coating selection can lead to improved tool life, reduced production costs, and more consistent weld quality.
Process parameters optimization for FSW
Optimizing process parameters is crucial for achieving high-quality friction stir welds. The interplay between various parameters significantly influences weld formation, microstructure, and mechanical properties. Key process parameters that require careful consideration and optimization include rotational speed, traversing speed, axial force, and tool tilt angle.
Rotational and traversing speed relationships
The relationship between rotational speed and traversing speed is fundamental to the FSW process. These parameters directly affect heat input, material flow, and weld quality. Generally, higher rotational speeds generate more heat, while faster traversing speeds reduce heat input per unit length of weld.
Optimizing the ratio of rotational to traversing speed is crucial for achieving the desired weld properties. A common metric used is the weld pitch, defined as the distance traveled per revolution:
Weld Pitch = Traversing Speed / Rotational Speed
Finding the optimal weld pitch for a given material and thickness is essential for balancing heat input, material flow, and weld strength. Too high a weld pitch may result in insufficient heating and poor material mixing, while too low a pitch can lead to excessive heat input and material softening.
Axial force and plunge depth control
The axial force applied to the FSW tool and the plunge depth are critical parameters that affect weld formation and quality. Proper control of these parameters ensures adequate material consolidation and prevents defects such as lack of penetration or excessive flash formation.
Axial force must be sufficient to maintain contact between the tool shoulder and the workpiece surface, generating enough frictional heat for material plasticization. However, excessive force can lead to tool wear and workpiece deformation. Advanced FSW systems often employ force-controlled welding, where the axial force is maintained at a set value throughout the process.
Plunge depth control is equally important, as it determines the engagement of the tool shoulder with the workpiece surface. Optimal plunge depth ensures proper heat generation and material containment while minimizing flash formation.
Tilt angle effects on weld quality
The tilt angle of the FSW tool, typically between 0° and 3°, can have a significant impact on weld quality and material flow. A slight tilt angle, with the rear of the tool lower than the front, can improve material consolidation and reduce defects.
The effects of tilt angle include:
- Enhanced material flow from the leading edge to the trailing edge of the tool
- Improved surface finish due to better forging action of the shoulder
- Reduced likelihood of void formation at the root of the weld
Optimizing the tilt angle requires consideration of factors such as material thickness, alloy type, and welding speed. In some cases, a zero tilt angle may be preferred, particularly when using specialized tool designs or for certain automated welding applications.
Thermal management in FSW processes
Effective thermal management is crucial for maintaining consistent weld quality and preventing overheating or underheating of the workpiece. Strategies for thermal management in FSW include:
- Active cooling systems: Using cooling fluids or gases to control workpiece and tool temperatures
- Adaptive control systems: Real-time adjustment of welding parameters based on temperature feedback
- Preheating techniques: For materials with high thermal conductivity or thick sections
Proper thermal management can lead to improved weld quality, reduced residual stresses, and enhanced tool life. It is particularly important when welding materials with different thermal properties or in applications where precise temperature control is critical for achieving desired microstructures and mechanical properties.
Advanced FSW techniques and variants
As friction stir welding technology has matured, several advanced techniques and variants have emerged to address specific challenges and expand the applicability of the process. These innovations offer improved performance, efficiency, and versatility in various welding scenarios.
Bobbin tool friction stir welding
Bobbin tool FSW, also known as self-reacting FSW, uses a tool with two shoulders connected by a pin. This configuration eliminates the need for a backing plate and allows for welding of closed sections or hollow profiles. Advantages of bobbin tool FSW include:
- Balanced forces on both sides of the workpiece, reducing distortion
- Improved weld symmetry and reduced risk of root defects
- Ability to weld complex geometries and hollow sections
This technique is particularly useful in industries such as shipbuilding and aerospace, where welding of large, complex structures is common.
Stationary shoulder friction stir welding
Stationary shoulder FSW uses a non-rotating shoulder with a rotating pin. This configuration offers several advantages:
- Reduced heat input and narrower heat-affected zone
- Improved surface finish due to the absence of shoulder-induced material flow
- Capability to weld higher melting point materials and dissimilar metal combinations
This technique is particularly beneficial for welding heat-sensitive materials or in applications where minimizing heat input and distortion is critical.
Ultrasonic-assisted friction stir welding
Integrating ultrasonic vibrations into the FSW process can enhance material flow and reduce welding forces. Benefits of ultrasonic-assisted FSW include:
- Improved material plasticization and mixing
- Reduced welding forces and tool wear
- Enhanced weld quality and mechanical properties
This technique shows promise for welding high-strength materials and for improving process efficiency in various FSW applications.
Friction stir spot welding applications
Friction stir spot welding (FSSW) is a variant of FSW used for creating localized spot welds. It is particularly useful in automotive and aerospace industries as an alternative to resistance spot welding. FSSW offers advantages such as:
- Lower energy consumption compared to resistance spot welding
- Ability to join dissimilar materials and aluminum alloys
- Improved fatigue performance of spot-welded joints
Recent developments in FSSW include refill techniques that eliminate the exit hole, further enhancing its applicability in visible areas of structures.
FSW equipment and machinery
The selection and configuration of FSW equipment play a crucial role in process capability, efficiency, and weld quality. From specialized FSW machines to adapted CNC systems and robotic welding cells, a range of equipment options are available to suit various production requirements.
Cnc-based FSW machines: capabilities and limitations
CNC-based FSW machines offer precision control and flexibility for a wide range of welding applications. These machines typically feature:
- High stiffness and load-bearing capacity to withstand FSW forces
- Precise control of tool position, speed, and force
- Capability for complex weld path programming
While CNC-based systems offer excellent precision and repeatability, they may have limitations in terms of workspace size and the ability to weld complex three-dimensional parts. The choice between a dedicated FSW machine and an adapted CNC system depends on production volume, part complexity, and required process flexibility.
Robotic FSW systems for complex geometries
Robotic FSW systems offer enhanced flexibility for welding complex geometries and large structures. These systems combine the versatility of industrial robots with specialized FSW end-effectors. Advantages of robotic FSW include:
- Ability to weld complex 3D paths and contours
- Flexibility to adapt to different part geometries and sizes
- Potential for integration with other automated processes
However, robotic systems may face challenges in terms of stiffness and force capacity compared to dedicated FSW machines. Advanced control algorithms and specialized robot designs are being developed to address these limitations and expand the capabilities of robotic FSW.
Force control systems in FSW equipment
Force control is a critical aspect of FSW equipment, ensuring consistent weld quality and tool engagement. Advanced FSW systems incorporate force control mechanisms that can:
- Maintain constant axial force throughout the weld
- Adapt to variations in material thickness or properties
- Provide real-time feedback for process monitoring and control
Force control systems may use hydraulic, pneumatic, or electromechanical actuators, often in combination with sophisticated sensor arrays and control algorithms. The integration of force control with position control allows for optimized welding parameters and improved weld quality consistency.
Quality assurance and testing methods for FSW joints
Ensuring the quality and integrity of friction stir welded joints is crucial for their successful implementation in critical applications. A comprehensive quality assurance program typically involves a combination of non-destructive testing, mechanical property evaluation, and microstructural analysis.
Non-destructive testing techniques for FSW
Non-destructive testing (NDT) methods play a vital role in assessing the quality of FSW joints without compromising their integrity. Common NDT techniques for FSW include:
- Ultrasonic testing: Effective for detecting internal defects such as voids or lack of penetration
- Radiographic inspection: Useful for identifying defects in thick sections or complex geometries
- Eddy current testing: Suitable for surface and near-surface defect detection
Advanced NDT
Advanced NDT methods such as phased array ultrasonic testing (PAUT) and computed tomography (CT) scanning are increasingly being used for more detailed inspection of FSW joints, particularly in critical applications.
Mechanical property evaluation of FSW joints
Evaluating the mechanical properties of FSW joints is essential for ensuring their performance in service conditions. Common mechanical testing methods include:
- Tensile testing: To determine strength and ductility of the welded joint
- Bend testing: To assess ductility and detect surface defects
- Hardness testing: To map hardness profiles across the weld zones
- Fatigue testing: To evaluate long-term performance under cyclic loading
These tests provide valuable data on the overall joint strength, ductility, and potential weak points in the weld structure. Comparing the mechanical properties of the welded joint to those of the base material helps in assessing the efficiency of the welding process.
Microstructural analysis of FSW weld zones
Microstructural analysis is crucial for understanding the complex material transformations that occur during FSW. The weld zone typically consists of distinct regions:
- Stir zone (SZ): The fully recrystallized region where material mixing occurs
- Thermomechanically affected zone (TMAZ): The region adjacent to the SZ, characterized by deformed grains
- Heat-affected zone (HAZ): The region affected by heat but not by plastic deformation
Techniques used for microstructural analysis include:
- Optical microscopy: For general microstructure observation
- Scanning electron microscopy (SEM): For high-resolution imaging and elemental analysis
- Transmission electron microscopy (TEM): For detailed analysis of grain structures and precipitates
- Electron backscatter diffraction (EBSD): For texture analysis and grain orientation mapping
Microstructural analysis provides insights into grain refinement, precipitate distribution, and texture evolution in FSW joints. This information is crucial for optimizing welding parameters and predicting joint performance under various loading conditions.
By combining non-destructive testing, mechanical property evaluation, and microstructural analysis, manufacturers can ensure the quality and reliability of FSW joints in critical applications. This comprehensive approach to quality assurance is essential for the continued adoption and expansion of FSW technology across various industries.